MAKE SURE YOU READ THIS ALL THE WAY THROUGH BEFORE STARTING THE JOB, JUST SO YOU DON'T GET AHEAD OF YOURSELF.
So to this point, you should have your Instrument Cluster in your hot little hands. Here is a picture of what it looks like out of the car, before taking it apart to get to the circuit board.
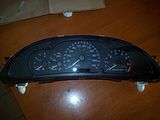
I regret that I forgot to take some pictures of the clips that hold the Cluster together, but once you have yours out of the car, you should be able to figure out how to get it apart. It is pretty obvious.
The main reason the gauges, speedometer and tachometer fail on these cars is due to faulty "Stepper Motors". Long gone is the day of speedometer and tachometer cables and real gauges that took information from sending units. All of that information nowadays is sent by electrical impulses to the Stepper Motor and then displayed on your Cluster.
This is a picture of what the Stepper Motor looks like. The one on the left is the Updated replacement to the one on the right. You can see the GM part number for the new motor... X25.168.
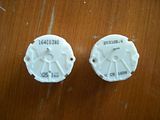
These shots of the Stepper Motors give you a better idea of what they look like.
Front side showing the shaft that the needle attaches to.
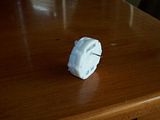
Rear side showing the two white indexing pins and the four wires you solder to the PCB (printed circuit board).
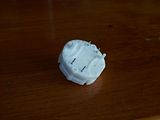
Now for the repair steps.
Once you have removed the clear plastic front to the cluster and the back cover that protects the circuit board this is what you will see.
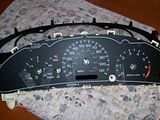
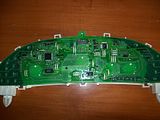
You can see on the face of the gauges in the previous pictures that I have placed tape near the starting point for the gauges, speedometer and tachometer. This is done to mark the location of the needles prior to pulling them off of the Stepper Motor Shaft. I couldn't find any masking tape, so I used Scotch Tape. Just make sure you can write on the tape. To get the needles to the correct position, you turn them slowly and gently counter clockwise until they stop. That should be the starting or resting point for them. Once you have all the needles to that position, go ahead and mark the needle position on the tape you stuck to the gauge faces.
Here is a close up of my son's cluster so you can see the marks I made. I wish I had taken a photo or two of the cluster prior to removing the needles so you could see how bad they were. The Temperature and Fuel gauge were pointing to the six o'clock position and the Speedometer was registering about 45 mph when the car was parked and not running. The only gauge working was the Tachometer.
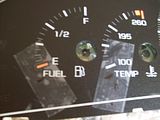
Once you have the needle positions marked on the tape, it is time to remove the needle from the shaft of each Stepper Motor. The instructions I followed were included with the motors I got on Ebay. Take each needle and turn it slowly counter clockwise until you feel it break loose from the Stepper Motor shaft. Don't worry, it shouldn't break, mine didn't. Once all of the needles are loose, take a Dinner Fork and place it under the base of the needle. Slowly and gently pull up on the needle to get it off of the shaft. It's a bit scary, I know, but it works just as I've written it. Remember which needle came off of which gauge so you put them back on the way they were.
You should be able to pull the cluster face off now. I didn't get a picture of the side of the PCB with the Motors on it. It's not really important since you work off the back side when removing the motors.
The following pictures show you the locations of the Stepper Motors on the business side of the board (soldered joints).
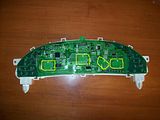
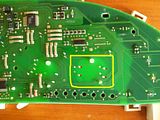
The first picture shows location of the four motors, see the yellow outlines. (If you want to see larger pictures, just click on whatever picture you want to see larger and you will see the larger size.) If you look closely, you can see the outlines of the motors through the PCB.
The second picture is just a close up of one of the motors on the board. You can see the outline of the motor more clearly in this picture. You can also see the two indexing pins that locate the motor properly on the PCB. I put a little red dot next to the soldering points on the PCB for the motor. These are the spots you will need to work on. It is quite easy to locate these spots for each of the four motors if you have the PCB in front of you.
Now all you have to do is remove the motors and solder in the new ones. I know, it sounds like a tough job, but it really isn't. I have a very basic knowledge of soldering and it only took me about 20 minutes to do the job.
What you have to have to complete the job is a soldering iron and some way to de-solder the joints. I bought a De-soldering Iron at Radio Shack for $11. It is extremely easy to use and makes the job a snap. I would guess it took me less than five minutes to remove all of the motors from the PCB using the De-soldering Iron.
Here is a picture of the De-soldering Iron.
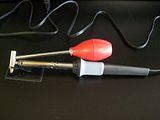
As you can see, it is nothing more than a soldering iron with a suction bulb attached. You squeeze the bulb, put the tip on the joint, let it heat for about 3-4 seconds and let the bulb go and remove the tip. Very simple. Just follow the instructions with the Iron. Also, there are several very good de-soldering videos on youtube you can watch, I found several, so go there and look if you want more information.
Once you have all the motors removed, you need to get the new motors in place for soldering. Make sure the wire pins go into their respective holes without folding under. They need to be sticking out through the holes to solder them in place. Just take your time, it isn't hard. Once the new motors are back in place, solder them all up. Again, youtube has several good soldering videos to help you out. I bought a nice little 30w Iron at Harbor Freight for $4 and it worked perfectly.
Here is a picture of the one I bought.
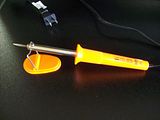
Make sure you have a pencil type tip, it makes it easier to get around those small joints. Here is a close up of the pencil tip:
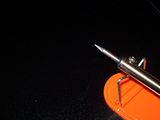
When soldering on a PCB, use 60/40 ROSIN core solder. Do NOT use acid core solder unless you want to ruin your circuit board. I bought some .032" solder. The smaller diameter makes it melt quicker, not as much mass to heat up.
This is the solder I used:
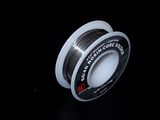
The soldering probably took me about 10 minutes or so to complete.
Once the soldering is done, you can put the Cluster back together. Just reverse the steps you did to take it apart. When you are ready to put the gauge needles back on, here is how you do it.
Put the needle on the shaft at the 12 o'clock position and push it on. Once they are all installed, turn the needle counter clockwise until you line up the needle with the mark you made on the tape. When you get to the mark, stop. That should be where each needle is at rest. You can put the rest of the cluster back together and get ready to put it back into the car.
As I stated in my previous blog entry on removal of the Dash on the Cavalier. I removed the fuses for the Instrument Cluster and the Air Bags. If you didn't follow my instructions regarding the Dash, I would suggest you remove those two fuses just to be safe.
Now, go out to the car and put the Cluster back where it is supposed to be and hook up the plug to the back. Now, put the Instrument Cluster fuse back in and you should see your needles set themselves to their resting points. If everything looks good, go ahead and put everything back together. When we did this on my son's car, the Speedometer was reading about 1 mph. We pulled the fuse, removed the cluster and opened it up. Moved the needle a little bit more counter clockwise and then put it back together. This time it was in the right spot.
We finished up by putting the dash back together and then starting the car. Everything seemed to be working correctly. Here is a picture of the Cluster while we were driving around checking it out.
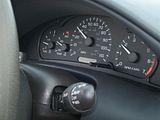
As you can see, everything seemed to be working properly. We used a GPS to make sure the Speedometer was working right and it was right on.
This little repair could cost you upwards of $500 if you have someone repair it for you. Even with buying the Soldering Iron, De-Soldering Iron, Solder and Motors, we had just under $60 into the repair.
Good Luck if you try this out.